CSA Z1004-12 pdf download – Workplace ergonomics — A management and implementation Standard.
2 Reference publications This Standard refers to the following publications, and where such reference is made, it shall be to the edition listed below. CSA (Canadian Standards Association) CAN/CSA-ISO 1 901 1 -03 (R2007) Guidelines for quality and/or environmental management systems auditing CAN/CSA-Z1 000-06 (R201 1 ) Occupational health and safety management ACGIH (American Conference of Governmental Industrial Hygienists) TLVs and BEIs (201 1 ) ASHRAE (American Society of Heating, Refrigerating and Air-conditioning Engineers) ANSI/ASHRAE 55-201 0 Thermal Environmental Conditions for Human Occupancy IES (Illuminating Engineering Society) The Lighting Handbook, 1 0th edition (201 1 ) INPO (Institute of Nuclear Power Operationist) 06-003 (2006) Human Performance Reference Manual ISO (International Organization for Standardization) ISO 6385:2004 Ergonomic principles in the design of work systems NIOSH (National Institute for Occupational Safety and Health) NIOSH Lifting Equation (1 991 )
3 Definitions The following definitions shall apply in this Standard: Anthropometry — the study of the size and shape of the human body. Note: Anthropometric data are one of the basic criterion used to design workspaces/tools/equipment to a range of body sizes and shapes. Application of Ergonomics — the use of ergonomics principles to identify and eliminate hazards and assess and control risks at each stage of design of any work system to enhance worker health, safety, and well-being and optimize system performance. It is an element of the Ergonomic Process. Audit — the systematic and documented process for obtaining evidence and evaluating it objectively to determine the extent to which the specified criteria are fulfilled. Cognitive — related to “cognition”, which is (a) the process people use for remembering, awareness, perception, reasoning, understanding, and using judgment; and (b) the ability to think and make sense out of what is seen, heard, felt, and experienced in order to take appropriate actions. Cognitive demands — stressors associated with cognitive aspects of tasks being performed (see Cognitive). Competence — demonstrated ability to apply ergonomics knowledge and skills to a work system design and operation. Competent person — a person who is knowledgeable of ergonomics by reason of education, training, experience, or a combination thereof, and has a demonstrated ability to apply this knowledge to the design and operation of work systems. Continual improvement — the process of enhancing the Ergonomics Process to achieve ongoing improvement in overall OHS performance. Design — the process of changing existing or developing new work systems, encompassing individual tasks through to complex systems. Document — a medium containing information related to the Ergonomics Process.
Ergonomics — the scientific discipline concerned with the understanding of interactions among humans and other elements of a system, and the profession that applies theory, principles, data, and methods to design in order to enhance human well-being and optimize overall system performance. Note: Also referred to as “human factors”. Ergonomics Process — the commitment, leadership, planning, implementation, and continuous improvement necessary to identify and eliminate hazards and to assess and control risks using ergonomics principles. It operates within the OHMS, where one exists, and in the design and operation of new or existing work systems. Ergonomist — an individual whose knowledge and skills concern the analysis of human-system interaction and the design of the system in order to enhance human well-being and optimize overall system performance. Evidence-based — derived from a systematic process of identifying, appraising, and using research findings and workplace experience as the basis for decision making. Hazard — a source of potential harm to a worker. Human factors — see Ergonomics. Lagging indicators — a measurable factor, such as lost time injuries, that changes after health or safety has already begun to follow a particular pattern or trend. Note: Lagging indicators confirm long-term trends, but they do not predict them. Leading indicators — a measurable factor, such as preventive measures to eliminate hazards that changes before the incident, injury, or disorders occur and start to follow a particular pattern or trend. Note: Leading indicators can be used to predict changes in disorders and injuries, but are not always accurate. Legal requirements — requirements of applicable laws and, where applicable, provisions of the organization’s collective agreements that relate to occupational health and safety. Management system — a system governing the overall performance expectations within the work environment. Mock-up — a sample that emulates a final product or layout. CSA Z1004-12 pdf download.
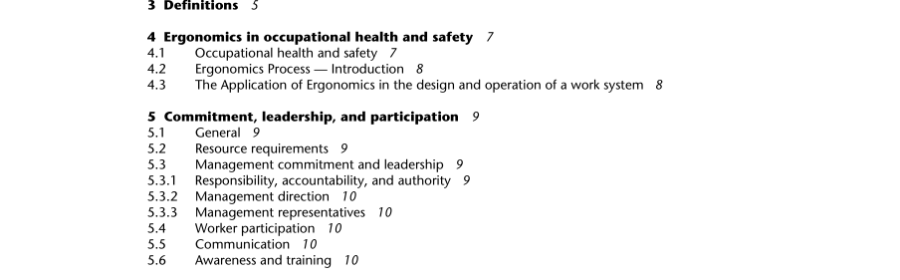